Recent Posts
-
Simple and clean is universally recognized beauty
Simple and clean is universally recognized beauty. On the market, some simple product clean but without beauty. Cause by the less refined of production process, and its related process control which can be sure to achieve it. At the moment of serious homogenization of products, this is one of the open secrets that distinguishes us from others. #Doorhardware#doorhandle#leverhandle#manufactory#Handlemanufactory#lockset#latch#StainlessSteelhandle#architecture
-
304SS PVD Gold lockset
304SS PVD Gold lockset. How much i love my own product, enjoy to just looking at them #doorhardware #doorhandle #manufactory #leverhandle #passlatch #lock #stainlesssteelhandle #architecture #mortiselock #lockset #latch
-
The richness of color lies not only in different colors
Satin black powder The richness of color lies not only in different colors. For example, do you know there are even lots of different "Black" ? #architecture #doorhandle #doorhardware #manufactory #leverhandle
-
Code: TH104UN/16 - Fire-rated handle. Pass 200,000 times recycle
Code: TH104UN/16. Appearance: - UnSpring function, 360 degree free turn. - Full stainless steel accessories. SS base & SS screws. - Fire-rated handle. Pass 200,000 times recycle. Need more information ? Please contact with us for full product sheet. #DoorHardware#DoorHandle#LeverHandle#StainlessSteelHandle#Architecture#EasyFixing#FastFix
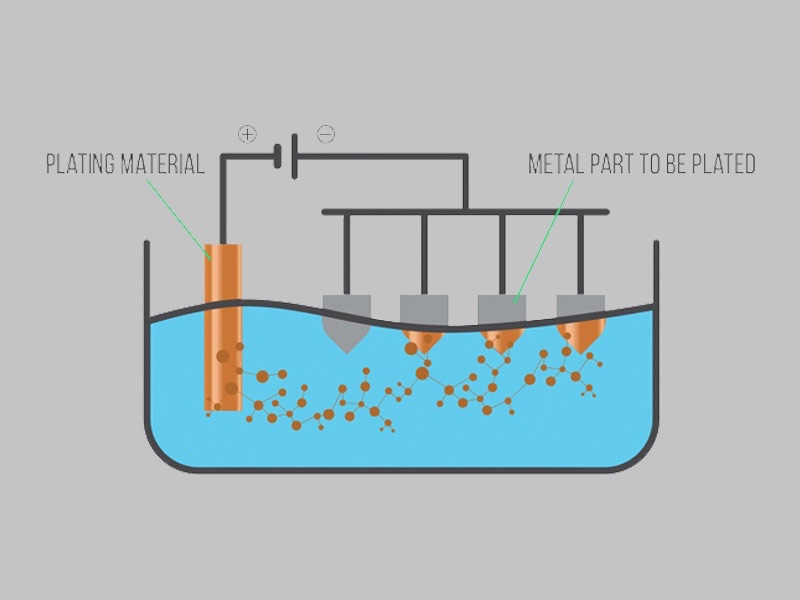
This document addresses issues related to internal components (iron-based parts) that require processing, electroplating, inspection, and assembly prior to installation. However, nonconforming electroplating results frequently occur during production.
Standard Nonconformance Handling Process:
1, Return defective components to the plating vendor.
2, The vendor must professionally strip all defective plating layers, perform thorough cleaning, and re-plate the components.
Unapproved Shortcut Practice:
Some suppliers occasionally use prohibited chemical agents to locally remove defective plating areas without full stripping, followed by direct re-plating. This method evades detection during routine inspections and standard salt spray testing (e.g., ASTM B117).
Latent Failure Case Study:
During a German port strike (3+ months container detention), components endured:
Extreme high temperatures (exceeding 50°C)
Excessive humidity (95% RH sustained)
High salinity levels (coastal atmospheric corrosion)
Result:
Complete internal rusting of iron components
Corrosion propagation to external stainless steel parts
Total product failure due to galvanic corrosion
Preventive Measures:
To mitigate such risks, we must:
Implement AS5553-based supplier quality protocols
Enforce cross-sectional microscopy verification for reworked parts
Conduct accelerated aging tests simulating 6-month marine exposure (per ISO 9223 CX-class)
Mandate electrochemical impedance spectroscopy (EIS) for coating integrity validation
This incident underscores the critical need for supplier process audits and enhanced corrosion protection standards in maritime applications.